In the brilliant galaxy of modern manufacturing, CNC gantry machining centers are like dazzling superstars, providing powerful machining capacity support for the development of numerous industries with their outstanding performance and wide range of applications.
CNC gantry machining centers mainly consist of gantry frames, worktables, crossbeams, rams, tool magazines, control systems, and other components. The gantry frame, as the supporting structure of the entire machine tool, has extremely high rigidity, which can ensure the stability of the machine tool during the machining process. The worktable is usually large and sturdy, capable of carrying workpieces with heavy weights and achieving precise movement in the longitudinal direction. The crossbeam moves up and down along the columns of the gantry frame, providing a vertical movement platform for the ram. The ram is responsible for moving horizontally on the crossbeam and carrying cutting tools for cutting, drilling, boring, milling, and other machining operations. The tool magazine is an important component for storing cutting tools and can automatically change tools according to machining requirements, enabling continuous operation of multiple machining processes.
Its working principle is based on the Computer Numerical Control (CNC) system. Operators first convert the three-dimensional model of the part to be machined into a CNC program through programming software. This program contains information such as tool paths, cutting parameters, and machining sequences. After the CNC system reads these programs, it precisely controls the movement of each coordinate axis (X, Y, Z axes, and sometimes including rotary axes), enabling the cutting tools to perform cutting, drilling, boring, milling, and other machining operations on the workpiece along the preset trajectories. During the machining process, sensors will monitor the running status of the machine tool in real time, such as tool wear and changes in cutting force, and feed back the information to the CNC system so that machining parameters can be adjusted in a timely manner to ensure machining precision and quality.
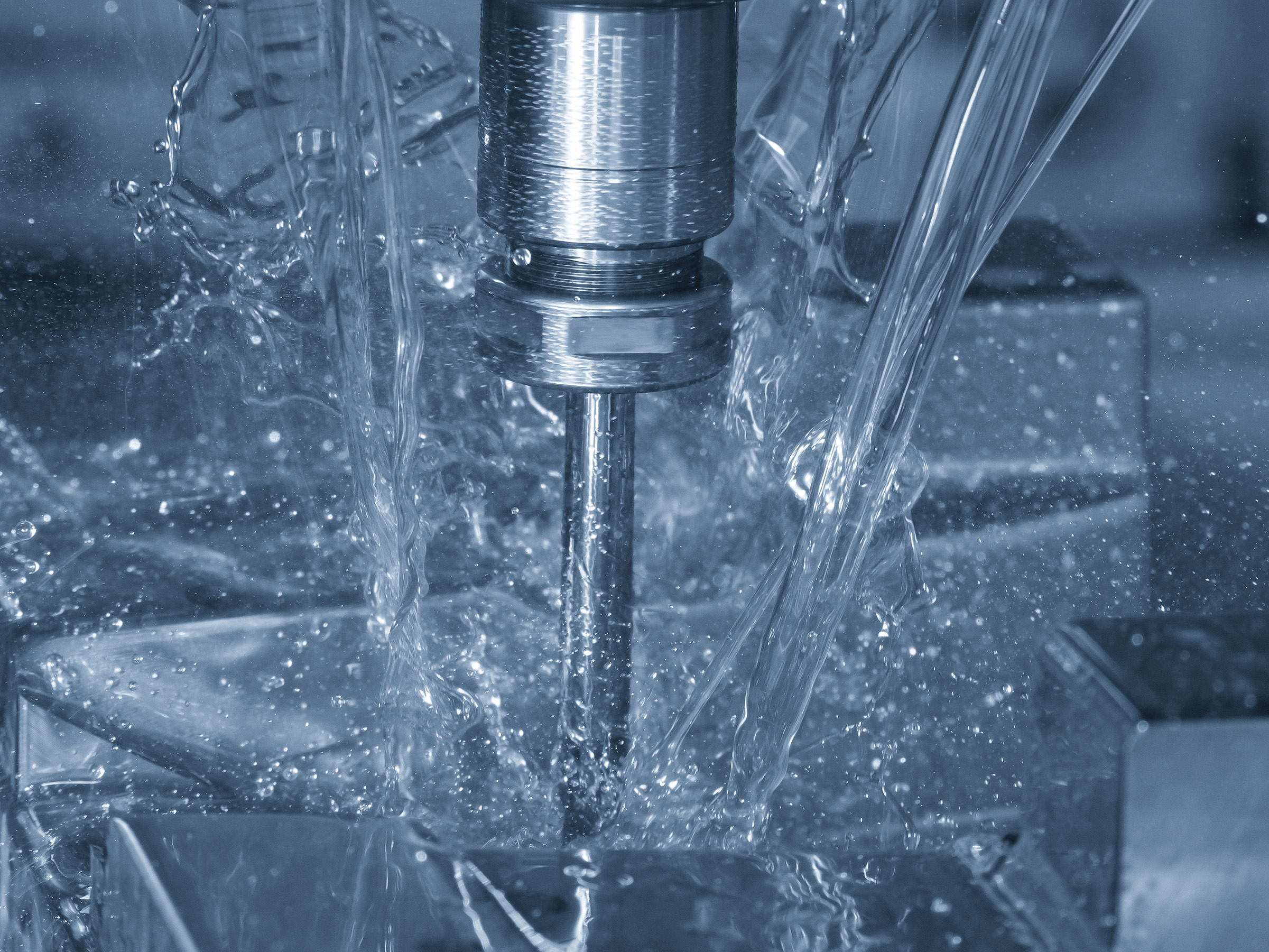
High-Precision Machining Capability
CNC gantry machining centers can achieve micron-level machining precision thanks to their precise transmission systems and advanced control systems. Their high-precision ball screws, linear guides, and high-performance servo motors ensure the accuracy of the movement of each axis. When machining workpieces with extremely high precision requirements, such as aerospace components and precision molds, they can meet strict dimensional tolerance and geometric tolerance requirements and produce high-quality products. For example, when machining large molds for aircraft wings, CNC gantry machining centers can precisely machine complex curved surfaces and high-precision positioning holes, providing an accurate mold foundation for the formation of aircraft wings.
High Rigidity and Large Load-Bearing Capacity
The gantry structure endows the machining center with extremely high rigidity, enabling it to withstand large cutting forces. Whether it is the machining of high-strength materials such as cemented carbide and titanium alloy or the machining of large workpieces, it can maintain a stable machining state. Its worktable with a large load-bearing capacity can place workpieces weighing several tons or even dozens of tons, making it suitable for the machining of large mechanical components, ship engine blocks, and other large workpieces. In the shipbuilding field, CNC gantry machining centers can easily machine the blocks of large ship engines and ensure that the machine tool will not deform due to the weight of the workpiece and cutting forces during the machining process.
High-Speed and High-Efficiency Machining
To meet the pursuit of production efficiency in modern manufacturing, CNC gantry machining centers adopt high-speed cutting technology. By increasing the spindle speed, feed rate, and acceleration, a large number of machining tasks can be completed in a short time. Meanwhile, the fast tool change function of the automatic tool changing system reduces the downtime during the machining process. When batch-producing large workpieces such as automotive parts, CNC gantry machining centers can quickly complete rough machining and finish machining, greatly shortening the production cycle and improving the production efficiency and economic benefits of enterprises.
Multi-Axis Linkage and Complex Curved Surface Machining Capability
Many CNC gantry machining centers have multi-axis linkage functions, such as four-axis and five-axis linkages. This multi-axis linkage capability enables the machine tool to machine various complex three-dimensional curved surfaces. In the fields of mold manufacturing and sculpture art reproduction, multi-axis linkage CNC gantry machining centers can precisely machine workpieces with complex shapes according to design models. For example, when manufacturing molds for automobile body panels, a five-axis linkage CNC gantry machining center can machine molds with smooth curved surfaces and precise contours, thus ensuring the high-quality forming of automobile body panels.
Aerospace Field
Aerospace components have extremely high requirements for precision, quality, and material performance. CNC gantry machining centers are used to machine key parts such as the fuselage frames, wing spars, and engine blades of aircraft. When machining engine blades, their high precision and multi-axis linkage functions can precisely machine the complex curved surfaces and internal cooling channels of the blades, ensuring that the blades have good performance under the harsh environment of high temperature, high pressure, and high-speed rotation. Meanwhile, when machining large aerospace structural parts, the large load-bearing capacity and high rigidity of CNC gantry machining centers can ensure the stability and precision of machining.
Automobile Manufacturing Field
The machining of large molds, engine blocks, transmission cases, and other components in automobile manufacturing is inseparable from CNC gantry machining centers. In terms of mold machining, it can quickly and precisely manufacture stamping molds for automobile bodies, ensuring the appearance quality and assembly precision of automobile bodies. For workpieces with complex structures such as engine blocks and transmission cases, CNC gantry machining centers can complete the machining of complex internal structures and high-precision hole systems through multi-axis linkage machining, improving the performance of engines and transmissions.
Mold Manufacturing Field
As the basic process equipment in manufacturing, the quality of molds directly affects the quality and production efficiency of products. CNC gantry machining centers are widely used in mold manufacturing. Whether it is plastic molds, die-casting molds, or stamping molds, they can all perform high-quality machining. They can machine the cavities, cores, sliders, and other parts of molds to meet complex shape and high-precision dimensional requirements. When machining high-precision injection molds, CNC gantry machining centers can ensure the surface finish and dimensional precision of the molds, thereby improving the quality and precision of plastic products.
Energy and Power Field
In the energy and power industry, CNC gantry machining centers are used to machine key components such as large generator rotors, stators, and turbine runners. These components are usually large in volume, heavy in weight, and have high precision requirements. The large load-bearing capacity and high-precision machining ability of CNC gantry machining centers can meet the machining requirements of these components and ensure the reliability and high efficiency of generators and turbines during operation. For example, when machining large turbine runners, CNC gantry machining centers can precisely machine the shapes of the blades and flow channels, improving the hydraulic efficiency of the turbines.
Intelligent Development
With the continuous development of artificial intelligence technology, CNC gantry machining centers will move towards the intelligent direction. Intelligent CNC systems will have the ability to learn and make decisions independently. They will be able to automatically adjust machining parameters, optimize tool paths, predict tool wear and machine tool failures according to real-time data during the machining process. For example, by analyzing data such as cutting force and vibration during the machining process through machine learning algorithms, the cutting speed and feed rate can be automatically adjusted to improve machining quality and efficiency while reducing human intervention and the labor intensity of operators.
Expansion of High-Precision and Micro-Nano Machining
In the future, the requirements for machining precision will continue to increase, and CNC gantry machining centers will seek breakthroughs in the field of micro-nano machining. By adopting more precise measurement systems, advanced control algorithms, and high-precision cutting tools, the machining of micro parts and microscopic structures will be achieved. In the fields of electronic information and biomedical, the demand for the machining of micro-nano structures is growing day by day. CNC gantry machining centers are expected to play an important role in these fields, such as machining micro-nano chips and biosensors.
Green and Sustainable Development
Against the background of the increasing awareness of environmental protection, CNC gantry machining centers will pay more attention to green and sustainable development. On the one hand, energy-saving motors, drivers, and control systems will be adopted to reduce the energy consumption of machine tools. On the other hand, the use of cutting fluid will be optimized, and dry cutting technology or minimum quantity lubrication cutting technology will be promoted to reduce the pollution of cutting fluid to the environment. In addition, more recyclable materials will be used in the design and manufacturing process of machine tools to achieve the sustainable development of machine tools.
Integration with the Industrial Internet
CNC gantry machining centers will be deeply integrated with the industrial internet to realize remote monitoring, fault diagnosis, and production data management of machine tools. By connecting machine tools to the network, manufacturers can obtain the running status, machining parameters, and production data of machine tools in real time and manage machine tools distributed in different regions in a unified manner. Meanwhile, by using big data analysis technology, the potential value in production data can be mined to provide a basis for enterprises' production decisions and further improve production efficiency and product quality.
In conclusion, as one of the core equipment in modern manufacturing, CNC gantry machining centers play an irreplaceable role in promoting the development of numerous industries with their unique structures, outstanding performances, and wide application fields. With the continuous progress of technology, they will continue to develop in the directions of intelligence, high precision, green and environmental protection, and integration with the industrial internet, bringing more innovations and breakthroughs to future manufacturing.