In the field of modern mechanical processing, CNC horizontal machining centers have become indispensable core equipment in precision manufacturing due to their unique structural design, excellent processing performance, and wide range of applications. They are like master craftsmen with exquisite skills, meticulously carving in the world of metals to create parts that meet high-precision requirements, injecting powerful impetus into the development of numerous industries.
CNC horizontal machining centers mainly consist of a machine bed, columns, a spindle headstock, a worktable, a tool magazine, a control system, and other components. The machine bed serves as the foundation of the entire machine tool, providing stable support to ensure that the machine tool does not experience significant displacement due to vibration or uneven force during the machining process. The columns are vertically installed on the machine bed, providing guidance and support for the up-and-down movement of the spindle headstock, guaranteeing the accuracy and stability of the spindle's movement in the vertical direction. Inside the spindle headstock, there is a high-precision spindle. The rotational movement of the spindle is the key to realizing the cutting processing of parts. It has a wide range of rotational speeds and high torque, enabling it to adapt to the requirements of different materials and processing techniques. The worktable is located on the machine bed and can perform precise indexing and positioning in the horizontal direction. It is used for clamping workpieces to be machined. Some advanced CNC horizontal machining centers also have a rotatable worktable, which can realize multi-sided machining, greatly improving machining efficiency and the machining precision of parts. The tool magazine is an important component for storing cutting tools. It usually can accommodate dozens or even hundreds of different types of cutting tools and can quickly and accurately change tools according to machining instructions, enabling the machine tool to complete multiple processes of machining with one clamping of the workpiece.
Its working principle is based on Computer Numerical Control (CNC) technology. Operators first write CNC programs using professional programming software according to the design drawings of parts. These programs specify in detail parameters such as the rotational speed of the spindle, the feed rate, the tool path, and the cutting depth during the machining process. After the CNC system reads these programs, it converts them into electrical signals to precisely control the movement of each coordinate axis of the machine tool (such as the X, Y, Z axes and rotary axes), so that the spindle drives the cutting tools to perform a series of machining operations such as cutting, drilling, boring, reaming, and tapping on the workpiece clamped on the worktable according to the predetermined trajectory. During the machining process, various sensors installed on the machine tool, such as position sensors and force sensors, monitor the running status and machining parameters of the machine tool in real time and feed back this information to the CNC system. The CNC system adjusts the machining parameters in a timely manner according to the feedback information to ensure the stability of the machining process and the consistency of the machining precision.
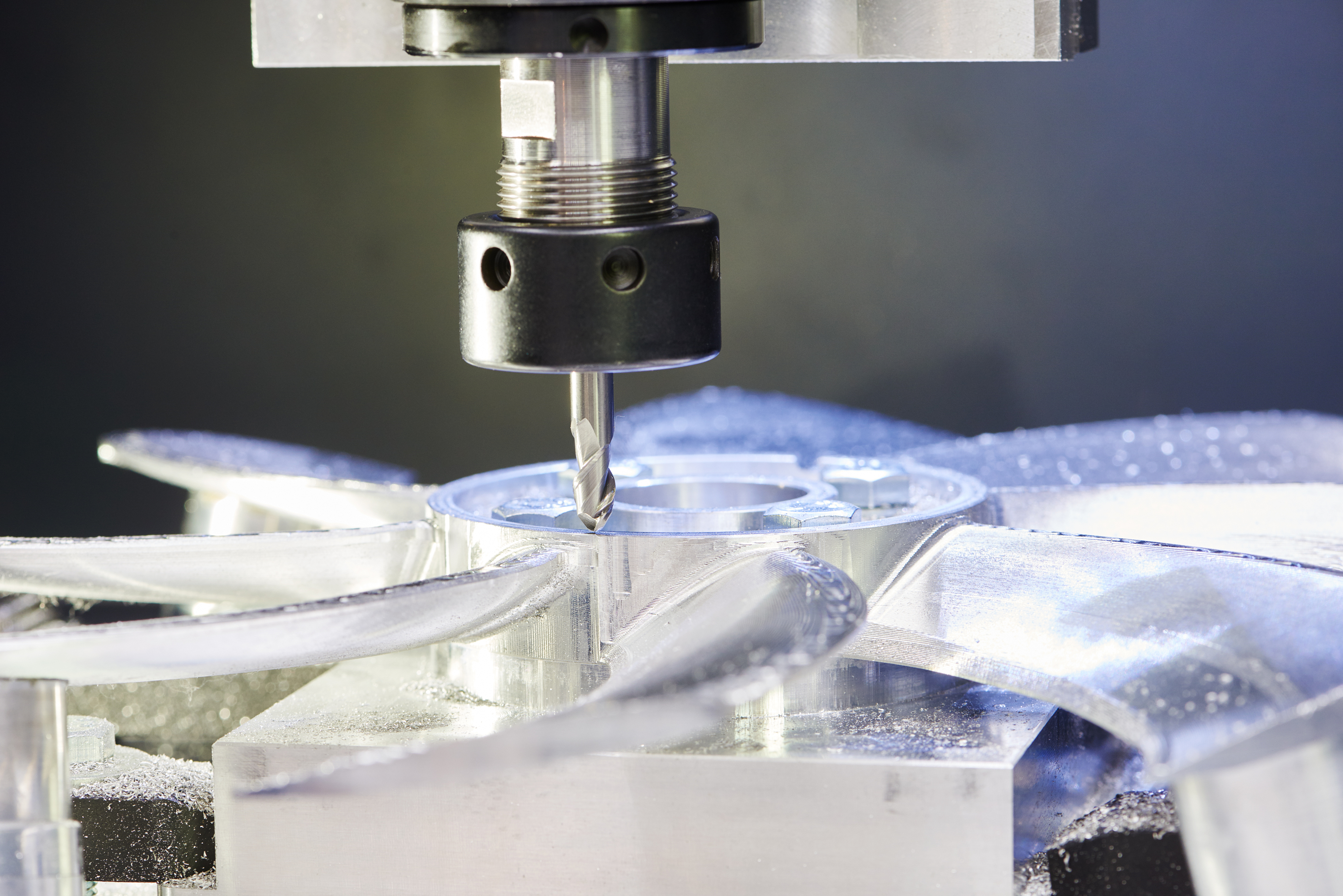
High-Precision Machining
CNC horizontal machining centers possess extremely high positioning precision and repeat positioning precision, usually reaching the micron level or even the sub-micron level. This is due to their precise transmission mechanisms, such as high-precision ball screws, linear guides, and advanced servo control systems. When machining parts with stringent precision requirements, such as aerospace components and precision molds, they can strictly ensure the dimensional tolerance and geometric tolerance requirements of the parts. For example, when manufacturing turbine blades for aircraft engines, CNC horizontal machining centers can precisely machine the complex curved surface shapes of the blades, ensuring the contour precision and surface quality of the blades, thereby improving the performance and reliability of the engine.
High Rigidity and Stability
Due to their structural design characteristics, CNC horizontal machining centers have excellent rigidity. During the machining process, they can effectively resist deformation caused by cutting forces and ensure the stability of machining precision. Especially when performing heavy cutting machining, the high rigidity advantage of the machine tool is more obvious. For example, when machining large steel castings or high-strength alloy parts, even under the action of large cutting forces, the machine tool can still maintain a stable working state to ensure that the machining quality is not affected.
High-Efficiency Machining Capability
The high efficiency of this machining center is manifested in multiple aspects. Firstly, its high-speed spindle can achieve relatively high rotational speeds. Combined with a large feed rate, it greatly shortens the machining time of individual parts. Secondly, the automatic tool changing system can complete tool changes within a very short time, reducing the downtime during the machining process. In addition, the characteristic of multi-process concentrated machining enables multiple machining operations to be completed after one clamping of the part, avoiding positioning errors caused by multiple clampings and further improving machining efficiency. In mass production industries such as automobile parts manufacturing, CNC horizontal machining centers can significantly improve production efficiency and reduce production costs.
Good Chip Removal Performance
The horizontal structural layout makes it easier for chips to be discharged from the working area of the machine tool under the action of gravity. This is not only beneficial for keeping the machining area clean, reducing the impact of chips on machining precision, but also effectively avoiding machine tool failures caused by chip accumulation. Good chip removal performance is particularly important when machining materials that generate a large amount of chips, such as aluminum, copper, and other non-ferrous metals, as it can ensure the continuity and stability of the machining process.
Aerospace Industry
The aerospace field has extremely high requirements for the quality and precision of parts. CNC horizontal machining centers play a crucial role in it. They are used to machine various key components of aircraft engines, such as casings, shaft parts, and disc parts. These parts usually have complex structures and high-precision requirements. CNC horizontal machining centers can ensure the machining quality of the parts through multi-axis linkage machining and high-precision cutting processes, meeting the operating requirements of aircraft engines under extreme working conditions such as high temperature, high pressure, and high speed. In addition, CNC horizontal machining centers are also widely used in the machining of aircraft fuselage structural parts, landing gears, and other components, providing a solid manufacturing guarantee for the development of the aerospace industry.
Automobile Manufacturing Industry
Automobile manufacturing is one of the important application fields of CNC horizontal machining centers. In the production of automobile engines, the machining of components such as cylinder blocks, cylinder heads, crankshafts, and camshafts is inseparable from CNC horizontal machining centers. They can efficiently and precisely complete various machining processes of these components, ensuring the performance and reliability of the engines. Meanwhile, in the manufacturing of automobile transmissions, chassis, and other components, CNC horizontal machining centers also play an important role. By improving machining precision and efficiency, they contribute to enhancing the overall quality and market competitiveness of automobiles.
Mold Manufacturing Field
As the basic process equipment in industrial production, the quality and precision of molds directly affect the molding quality and production efficiency of products. CNC horizontal machining centers have unique advantages in mold manufacturing and can machine mold cavities and cores with various complex shapes. Whether it is injection molds, die-casting molds, or stamping molds, they can realize high-precision machining of molds through multi-axis linkage machining and high-precision tool path control, ensuring the dimensional precision, surface quality, and demolding performance of the molds, thereby improving the service life of the molds and the quality of plastic products, metal die castings, and other products produced.
Construction Machinery Industry
In the construction machinery manufacturing, CNC horizontal machining centers are used to machine various large components, such as the slewing platform of excavators, the gearbox body of loaders, and the boom of cranes. These components are usually large in volume, heavy in weight, and have complex structures. The large worktable load-bearing capacity and high-rigid structure of CNC horizontal machining centers can meet their machining requirements. Through precise machining, the quality and performance of these components are ensured, improving the overall reliability and working efficiency of construction machinery.
Intelligent and Automated Development
With the continuous development of artificial intelligence, the Internet of Things, and other technologies, CNC horizontal machining centers will move towards intelligence and automation. Future CNC systems will have stronger intelligent decision-making capabilities, be able to automatically optimize machining parameters, select the best tool paths according to machining tasks, and monitor the running status of the machine tool in real time, predict possible failures and take preventive measures in advance. Meanwhile, the degree of automation will be further improved, such as realizing automatic loading and unloading, automatic inspection, and other functions, reducing human intervention and improving the stability of production efficiency and machining quality.
Expansion of High-Precision and Ultra-Precision Machining
To meet the increasing demand for part precision in high-end manufacturing, CNC horizontal machining centers will continue to explore high-precision and ultra-precision machining technologies. This will involve the research and development of higher-precision transmission components, advanced measurement and compensation technologies, and optimized control algorithms. Through breakthroughs in these technologies, it is expected to achieve nanometer-level machining precision, enabling the manufacturing of micro-nano structured parts with more excellent performance, which can be applied to cutting-edge fields such as electronic information and biomedical.
Application of Green and Environmentally Friendly Machining Technologies
In today's era of increasing environmental awareness, CNC horizontal machining centers will pay more attention to the application of green and environmentally friendly machining technologies. On the one hand, environmentally friendly cutting technologies such as dry cutting and minimum quantity lubrication cutting will be promoted to reduce the usage amount of cutting fluid and the pollution to the environment. On the other hand, in the design and manufacturing process of machine tools, energy-saving motors, drivers, and control systems will be adopted to improve the energy utilization efficiency of machine tools, reduce energy consumption, and achieve the goal of sustainable development.
Strengthening of Multi-Axis Linkage and Compound Machining Functions
The multi-axis linkage machining technology will be further developed and improved. CNC horizontal machining centers will have the ability of multi-axis linkage with more axes, such as linkage of more than five axes. This will enable them to machine more complex part shapes, improve the machining precision and surface quality of parts. Meanwhile, compound machining functions will be strengthened. Machine tools will integrate more processing techniques, such as turning, milling, grinding, laser processing, etc., realizing the completion of multiple machining processes with one clamping, reducing the transfer time of parts between different machine tools, improving production efficiency and machining precision.
In conclusion, CNC horizontal machining centers occupy a pivotal position in modern precision manufacturing due to their excellent performance characteristics and wide range of application fields. With the continuous progress of science and technology, their development trends such as intelligence, high precision, green and environmental protection, and compound machining will further promote the transformation and upgrading of the manufacturing industry, creating more value and opportunities for the development of the global industry.