In the high-tech aerospace field, the precision assurance of CNC machine tools is a crucial factor in ensuring the performance, safety, and reliability of aircraft and spacecraft. From the precision components of airplanes to the complex structural parts of spacecraft, every machining process has extremely high precision requirements, and CNC machine tools are tasked with fulfilling these precision requirements.
Aerospace materials usually possess characteristics such as high strength, high hardness, high temperature resistance, and lightweight, which pose significant challenges to the machining of CNC machine tools. For example, titanium alloys are widely used in the aerospace field due to their excellent strength-to-weight ratio, but they are difficult to machine. During the cutting process of titanium alloys, high temperatures are easily generated, leading to increased tool wear. Meanwhile, their high chemical reactivity makes them prone to chemical reactions with tool materials, affecting machining precision. To address these issues, CNC machine tools need to adopt special tool materials and cutting parameters. Advanced ceramic tools or carbide tool coating technologies are applied to the machining of titanium alloys. By rationally controlling cutting speed, feed rate, and cutting depth, the generation of cutting heat can be reduced, tool wear can be minimized, and thus machining precision can be ensured.
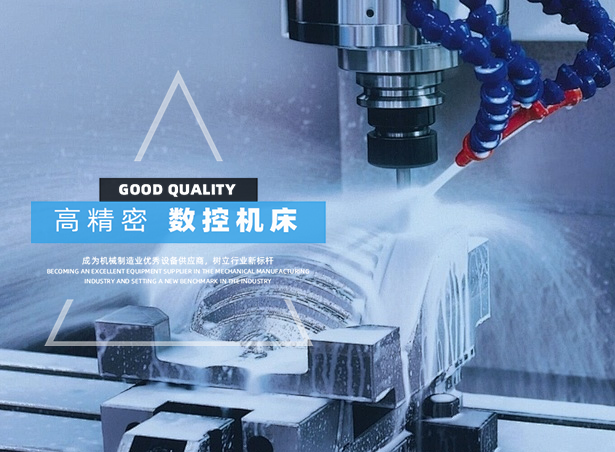
The structural design of CNC machine tools directly affects their precision stability. In aerospace machining, machine tools are required to have a high-rigid, high-precision motion system and good thermal stability. A high-rigid machine tool structure can withstand large cutting forces and reduce deformation during the machining process. High-quality cast iron materials or high-strength alloy materials are used to manufacture the machine tool bed, and through reasonable structural design, such as the arrangement of reinforcing ribs, the overall rigidity of the machine tool is enhanced. The high-precision motion system relies on precision components such as guide rails, lead screws, and servo motors. The precision of linear guide rails and ball screws directly determines the motion precision of the machine tool's coordinate axes, and high-performance servo motors can accurately control the motion position and speed of the machine tool. Additionally, the heat generated during aerospace machining can cause thermal expansion of machine tool components, thereby affecting machining precision. Therefore, CNC machine tools are usually equipped with cooling systems and thermal compensation devices. The cooling system can reduce the temperature of the machine tool and minimize thermal deformation; the thermal compensation device can monitor the temperature of the machine tool in real time and compensate for machining errors to ensure that the machine tool can maintain high machining precision under different temperature conditions.
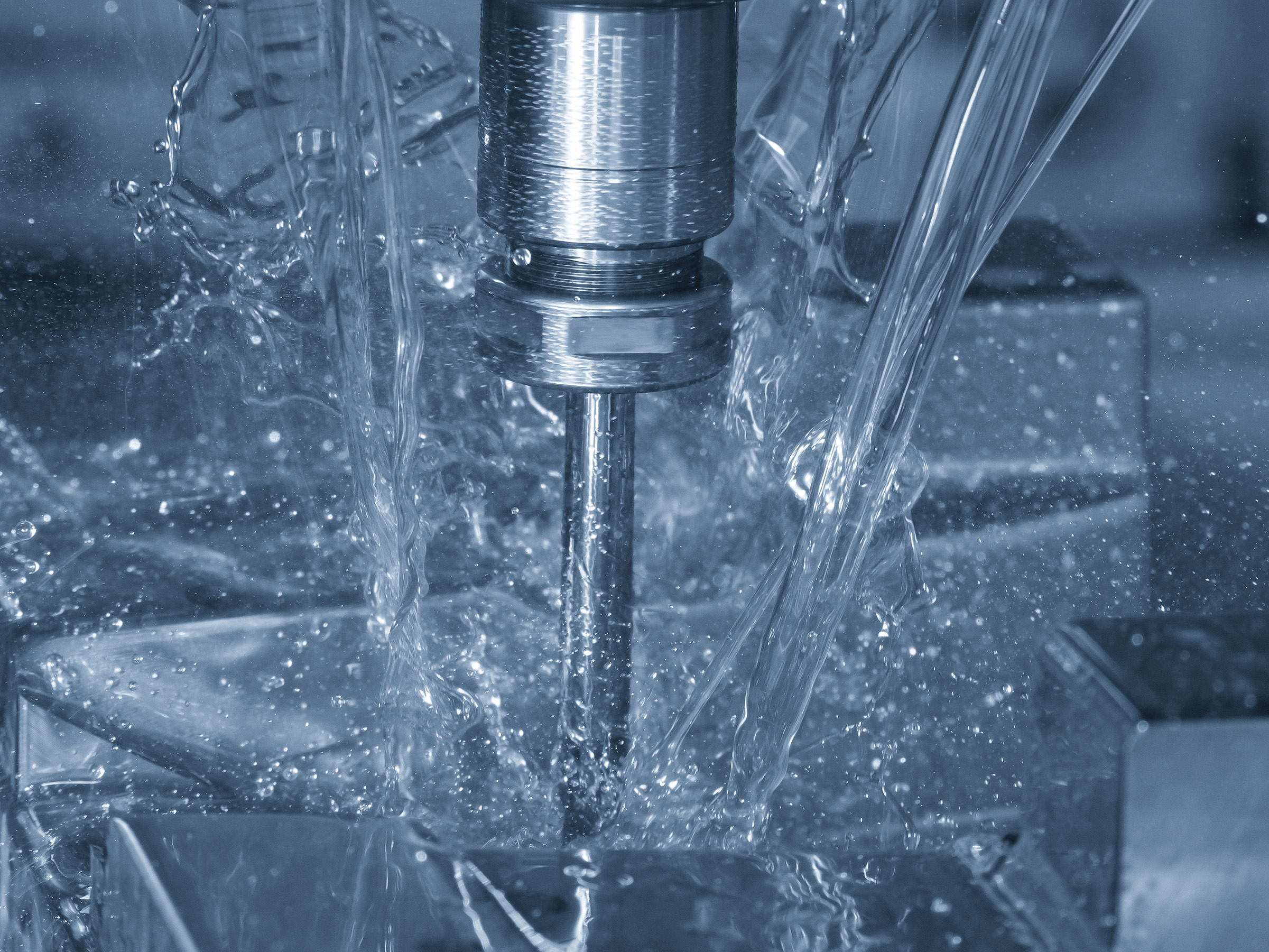
Accurate programming is an important prerequisite for achieving high-precision machining with CNC machine tools. In the aerospace field, the shapes of parts are complex and diverse, and multi-axis linkage machining is often required. Programmers need to formulate reasonable tool paths and machining processes based on the three-dimensional models of parts. Advanced Computer Aided Programming (CAM) software plays an important role in aerospace machining. It can automatically generate optimized tool paths, avoid interference between tools and parts, and take into account the balance between machining efficiency and precision. For example, when machining aircraft engine blades, CAM software can generate continuous and smooth tool trajectories according to the curved surface shape of the blades, ensuring the machining precision and surface finish of the blades. The control system of CNC machine tools is also a key link in precision assurance. A high-precision numerical control system can accurately interpret and execute programming instructions, controlling the motion precision of each axis of the machine tool to the micron or even sub-micron level. Meanwhile, the numerical control system also has an error compensation function. By monitoring and compensating for the positioning errors and backlash of the machine tool in real time, machining precision can further be improved. To ensure the stability and reliability of the control system, the aerospace field usually adopts dedicated high-performance numerical control systems and conducts strict testing and verification.
During the machining process of aerospace parts, strict inspection and quality control are important means to ensure precision. CNC machine tools are usually equipped with online inspection systems that can monitor parameters such as dimensional, shape, and positional precision during the machining process in real time. For example, using measurement devices such as laser interferometers or grating scales, the motion precision of the machine tool can be detected and fed back in real time, and machining errors can be detected and corrected in time. After the parts are machined, offline inspection is also required. A three-coordinate measuring machine is one of the commonly used inspection devices in the aerospace field. It can accurately measure the three-dimensional dimensions of parts and compare them with the design model to determine whether the parts meet the precision requirements. For key parts, non-destructive testing techniques such as ultrasonic testing and X-ray testing are also used to detect whether there are defects inside the parts, ensuring the quality and reliability of the parts. Additionally, establishing a complete quality control system is essential. From the inspection of raw materials to each process during the machining process and finally to the inspection of the final product, everything needs to be operated and monitored strictly according to quality standards to ensure that each part can meet the high-precision requirements of the aerospace field.
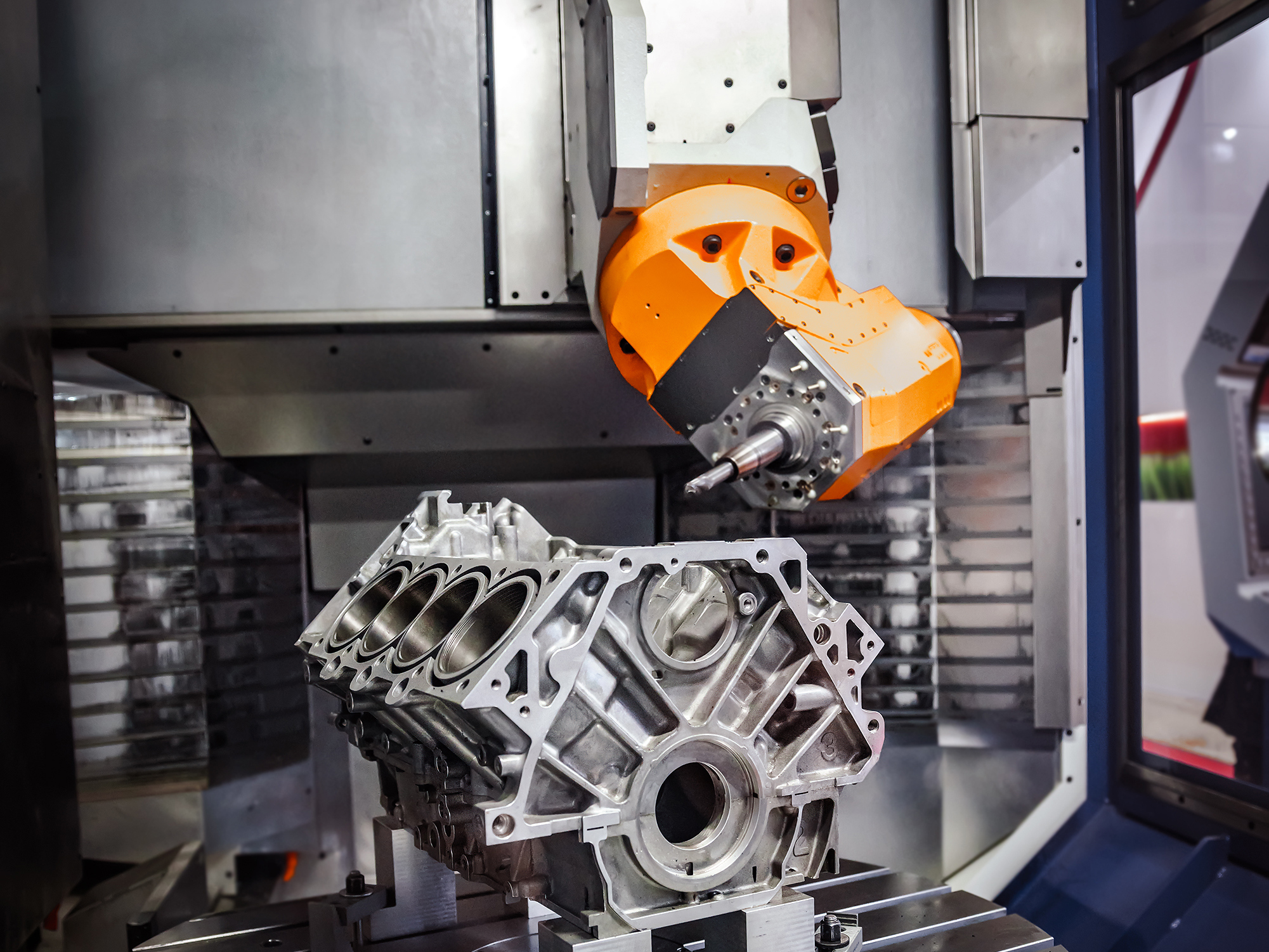
The aerospace manufacturing environment usually has a certain impact on the precision of CNC machine tools. For example, factors such as the temperature, humidity, and vibration in the workshop can cause changes in the precision of the machine tool. Temperature changes can lead to thermal expansion or contraction of machine tool components, thereby affecting the precision of machining dimensions. Therefore, aerospace manufacturing workshops usually need to implement constant temperature control to keep the temperature fluctuating within a certain range. Humidity also has an impact on the electrical system and metal components of the machine tool. Excessive humidity may cause electrical equipment failures and metal corrosion. Therefore, the workshop needs to be equipped with dehumidifying equipment to maintain a suitable humidity environment. Vibration is another important factor affecting the precision of the machine tool, especially during the precision machining of aerospace components, where even a tiny vibration can have a significant impact on machining precision. To reduce the impact of vibration, the machine tool can be installed on a vibration-isolating foundation and equipped with vibration-damping devices to reduce the transmission of external vibrations. Meanwhile, in the workshop layout and production arrangements, it is also necessary to consider avoiding the interference of vibrations generated by other equipment on CNC machine tools.
In conclusion, the precision assurance of CNC machine tools in the aerospace field is a systematic project involving multiple aspects such as materials, machine tool structure, programming and control, inspection and quality control, and the environment. Only by taking effective measures in each link can we ensure that CNC machine tools meet the required high-precision requirements in the machining of aerospace parts, providing solid support for the development of the aerospace industry. With the continuous progress of science and technology and the continuous increase in precision requirements in the aerospace field, the precision assurance technology of CNC machine tools will also continue to innovate and develop to meet more complex and strict machining requirements in the future.