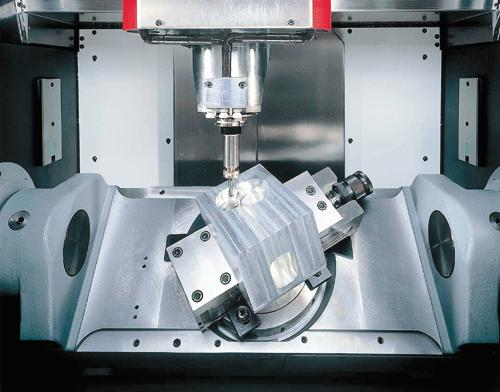
Aerospace manufacturing is renowned for its requirements of "high precision, difficult machining, and high reliability." The machining accuracy of complex structural components directly impacts the aerodynamic performance and safety of aircraft. With the maturation of five-axis simultaneous machining technology, numerous enterprises have achieved significant technological leaps in the manufacturing of critical components.
Materials commonly used in aerospace, such as titanium alloys and Inconel superalloys, feature high strength and poor thermal conductivity. According to research in Aeronautical Manufacturing Technology journal, during traditional machining processes, the tool wear rate for these materials is over four times higher than that of ordinary steel. Additionally, components like aircraft engine impellers and aerospace fuel tank brackets often have thin-walled, multi-curved structures, making it difficult for traditional three-axis machine tools to complete full-profile machining.
Take aerospace engine combustion chamber components as an example. The traditional process of "three-axis machining + manual grinding" not only results in long processing cycles but also struggles to meet stringent precision requirements. According to international aerospace standards, the contour error of aerospace components must be controlled within ±0.05mm, which traditional processes often exceed.
Technical Dimension | Three-Axis Machine Tools | Five-Axis Machining Centers |
---|
Number of Motion Axes | Linear motion along X/Y/Z axes | Additional A/C rotary axes for five-axis simultaneous motion |
Machining Capabilities | Planar and simple curved surfaces | Inclined surfaces at any angle, free-form surfaces |
Tool Orientation Control | Fixed-direction cutting | Real-time adjustment of cutting angles |
Typical Applications | Flat parts | Complex structures like impellers and blisks |
In practical applications, dual-tilting-head five-axis machine tools can complete full-circumference machining of impeller blades in a single setup, thanks to their flexible motion range. Meanwhile, the application of five-axis simultaneous interpolation algorithms, such as NURBS spline interpolation, significantly reduces machining path errors for complex curved surfaces.
After introducing five-axis machining centers, a certain aerospace manufacturing enterprise achieved remarkable results in engine blade machining, as reported publicly. By adopting layered cutting and optimizing tool paths, the enterprise improved production efficiency significantly for blade machining, which previously required multiple processes and long durations. The rejection rate decreased substantially, and the surface roughness reached industry-leading levels, meeting the assembly requirements of high-end aerospace engines.
Companies like Boeing have applied digital twin technology to optimize five-axis machining processes. By validating cutting schemes in virtual environments, they have effectively reduced process debugging time.
Green technologies such as cryogenic machining and dry cutting are becoming more prevalent. For example, cryogenic machining using liquid nitrogen cooling can extend tool life and reduce coolant usage. Dry cutting achieved through optimized tool coatings can significantly lower consumable costs.
Precision Matching Principle
According to the report by China Machine Tool & Tool Industry Association, for parts with tolerance requirements ≤±0.02mm, it is recommended to select five-axis equipment with a positioning accuracy ≤±0.005mm.
Evaluation of Service Systems
Enterprises should prioritize suppliers that offer "turnkey" services, including programming training and fault early warning systems, to prevent equipment idleness.
Total Cost of Ownership (TCO) Model
Although the initial investment for five-axis machine tools is relatively high, in the long run, the increased efficiency and reduced rejection rate can effectively lower the total cost of ownership.
Today, key components of new-generation aircraft such as the Airbus A350 and COMAC C919 are widely manufactured using five-axis machining technology. Five-axis machining centers have become core equipment in high-end aerospace manufacturing. For exclusive five-axis machining solutions in the aerospace industry, or to schedule material machining tests, please contact our technical expert team.