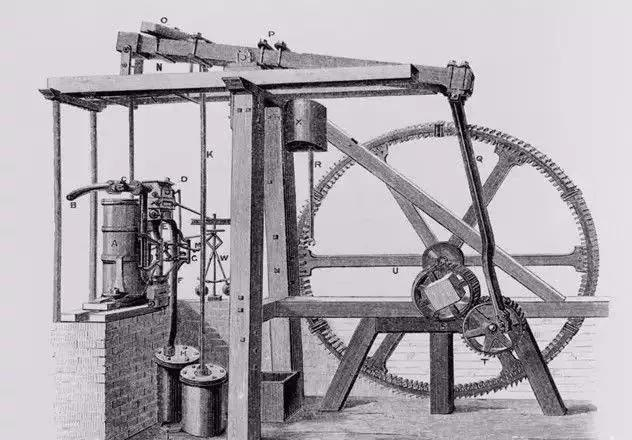
Against the backdrop of the global advocacy for green travel and sustainable development, the new energy vehicle industry is experiencing rapid growth, becoming a crucial direction for the transformation and upgrading of the automotive sector. In the production and manufacturing processes of new energy vehicle enterprises, machine tools play a pivotal role and serve as core equipment to ensure product quality and production efficiency.
The "Three-Electric Systems" of new energy vehicles—motor, electric control, and battery—are the vehicle's core components, imposing stringent requirements on machining precision, surface finish, and dimensional stability. Traditional machining techniques can no longer meet these demands. High-precision, high-speed, and high-yield advanced CNC machine tools have emerged as the ideal choice for processing the "Three-Electric Systems". For instance, during the machining of motor shafts and rotors, precision turning on CNC lathes can ensure the straightness and coaxiality of the motor shafts, enhancing the rotation accuracy of the motors. Precision milling of rotors enables accurate machining of the slot shapes, ensuring the matching precision between the rotor and stator and reducing energy losses.
The battery system, as the energy source of new energy vehicles, determines the safety and performance of the vehicles. Machine tools offer significant advantages in the machining of battery boxes and casings. Precision casting using CNC machine tools can produce battery boxes and casings with complex shapes and precise dimensions. Subsequently, CNC machining of the castings removes surface defects, ensuring dimensional accuracy and surface quality. In the machining of electric control components, precision milling creates accurate circuit board and electronic component mounting holes, while laser processing technology is employed to produce high-precision circuit patterns and connection lines, enhancing the electrical performance of the electric control components.
The machining of vehicle body components also relies on machine tools. CNC punching machines perform precision stamping, enabling the production of vehicle body structural components with complex shapes and precise dimensions. CNC welding equipment is used for welding vehicle body components, ensuring welding quality and strength. Additionally, in the machining of new energy vehicle components, such as those of the steering and suspension systems, machine tools play an irreplaceable role, ensuring the machining precision of each component and improving the overall vehicle performance.
With the continuous expansion of the new energy vehicle industry, the demand for machine tools will continue to grow. Meanwhile, higher requirements are put forward for the intelligence, automation, and high precision of machine tools. It can be foreseen that machine tools will continue to drive the new energy vehicle manufacturing field, propelling the industry towards higher-quality development.