In modern manufacturing, CNC lathes have become an indispensable key equipment due to their high precision, high efficiency, and high degree of automation. Let's review the development history of CNC lathes and explore its glorious transformation from birth to the present.
The origin of numerical control technology can be traced back to the middle of the 20th century. After World War II, the aircraft manufacturing industry had an increasing demand for processing complex-shaped parts. Traditional processing methods were difficult to meet the requirements of precision and efficiency. Thus, people began to seek a new processing technology, and numerical control technology came into being.
The early CNC lathes were hardwired numerical control systems composed of components such as electron tubes and relays. Although this system improved processing precision and efficiency to a certain extent, it had problems such as large volume, poor reliability, and complex programming. With the development of semiconductor technology, numerical control systems gradually adopted transistors and integrated circuits, greatly reducing the volume of the system and improving reliability.
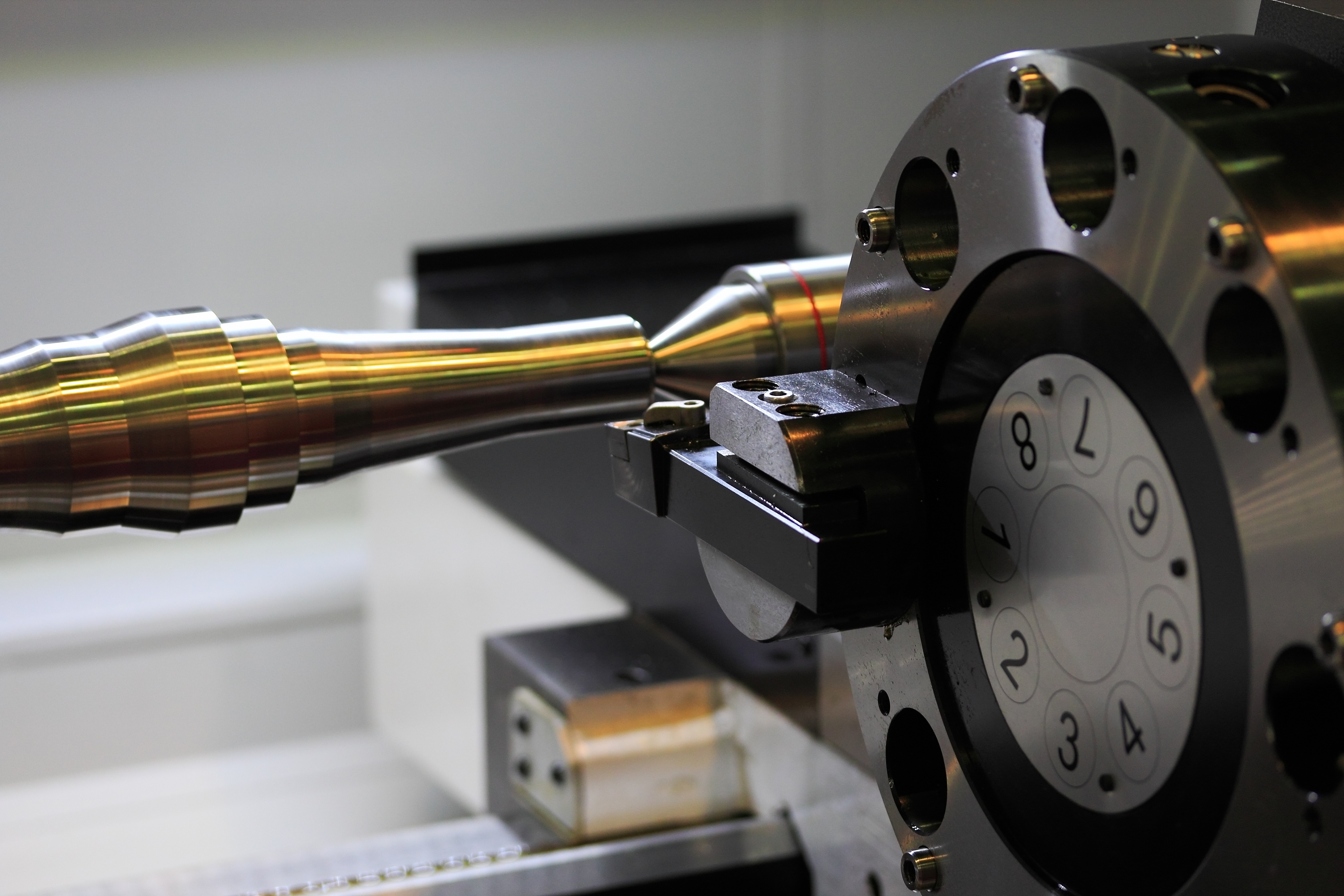
In the 1970s, computer technology began to be applied to numerical control systems, and computer numerical control (CNC) systems emerged. CNC systems have powerful computing capabilities and flexible programming functions, enabling the processing of complex parts. At the same time, the structure of CNC lathes is also constantly improving. Advanced transmission components such as ball screws and linear guides are adopted to improve the precision and speed of the machine tool.
Entering the 1980s, with the further development of microelectronics technology and automatic control technology, the performance of CNC lathes has been greatly improved. Multi-axis linkage CNC lathes appeared, which can simultaneously control the movement of multiple coordinate axes and realize the processing of complex curved surfaces. In addition, the degree of intelligence of numerical control systems is also constantly improving, with functions such as self-diagnosis and adaptive control, further improving processing quality and efficiency.
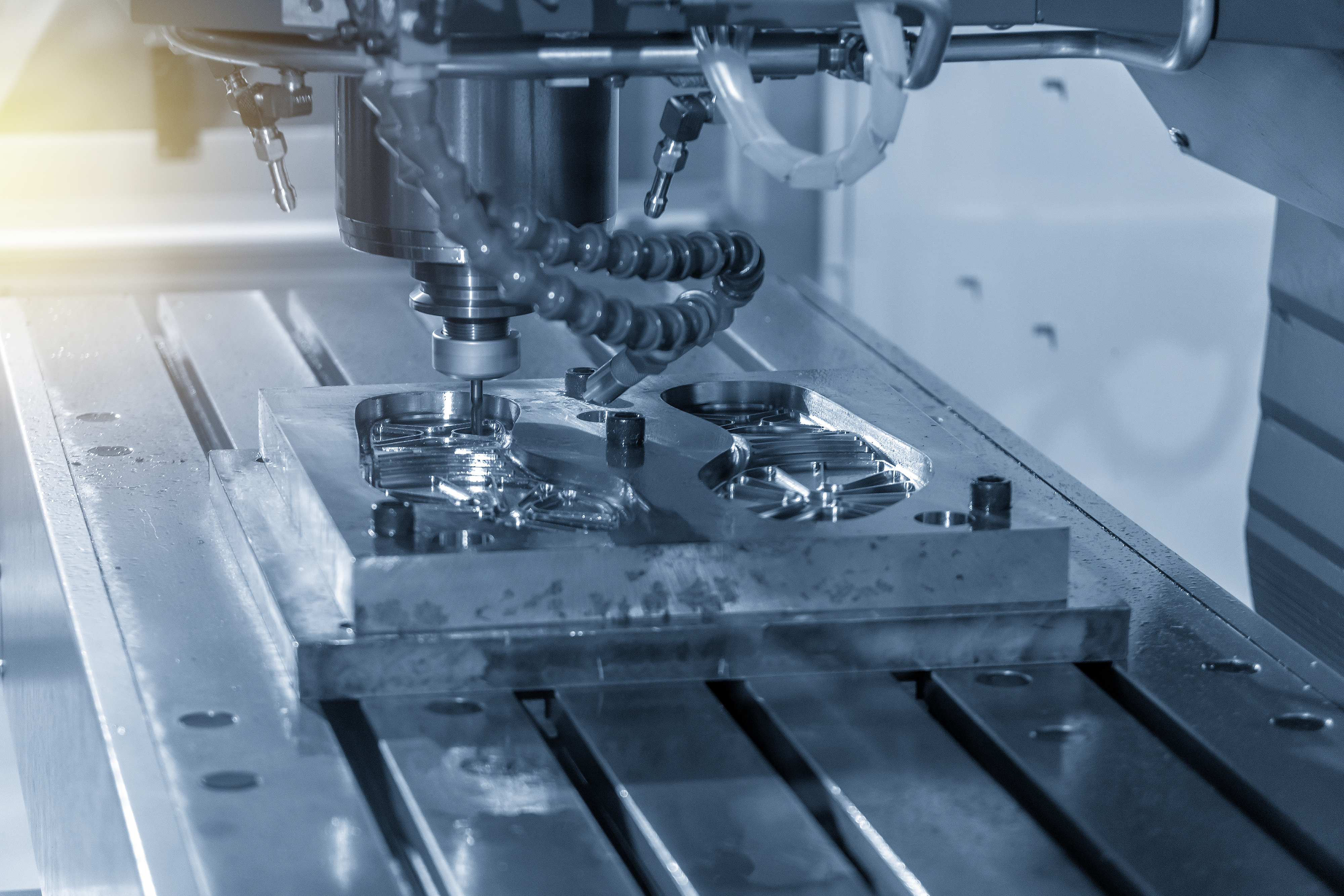
Since the 1990s, CNC lathes have been developing in the directions of high speed, high precision, high reliability, and multi-functionality. The application of high-speed cutting technology has greatly increased processing efficiency and also put forward higher requirements for the structure and control system of machine tools. To meet the needs of high-precision processing, CNC lathes have adopted error compensation technology and nanometer-level interpolation technology, making the processing precision reach the sub-micron or even nanometer level.
In today's era, CNC lathes have been widely used in various fields such as aerospace, automobile manufacturing, and mold processing. With the development of intelligent manufacturing technology, CNC lathes are also constantly developing towards intelligence, networking, and integration. Future CNC lathes will be more intelligent, efficient, and environmentally friendly, making greater contributions to the development of the manufacturing industry.
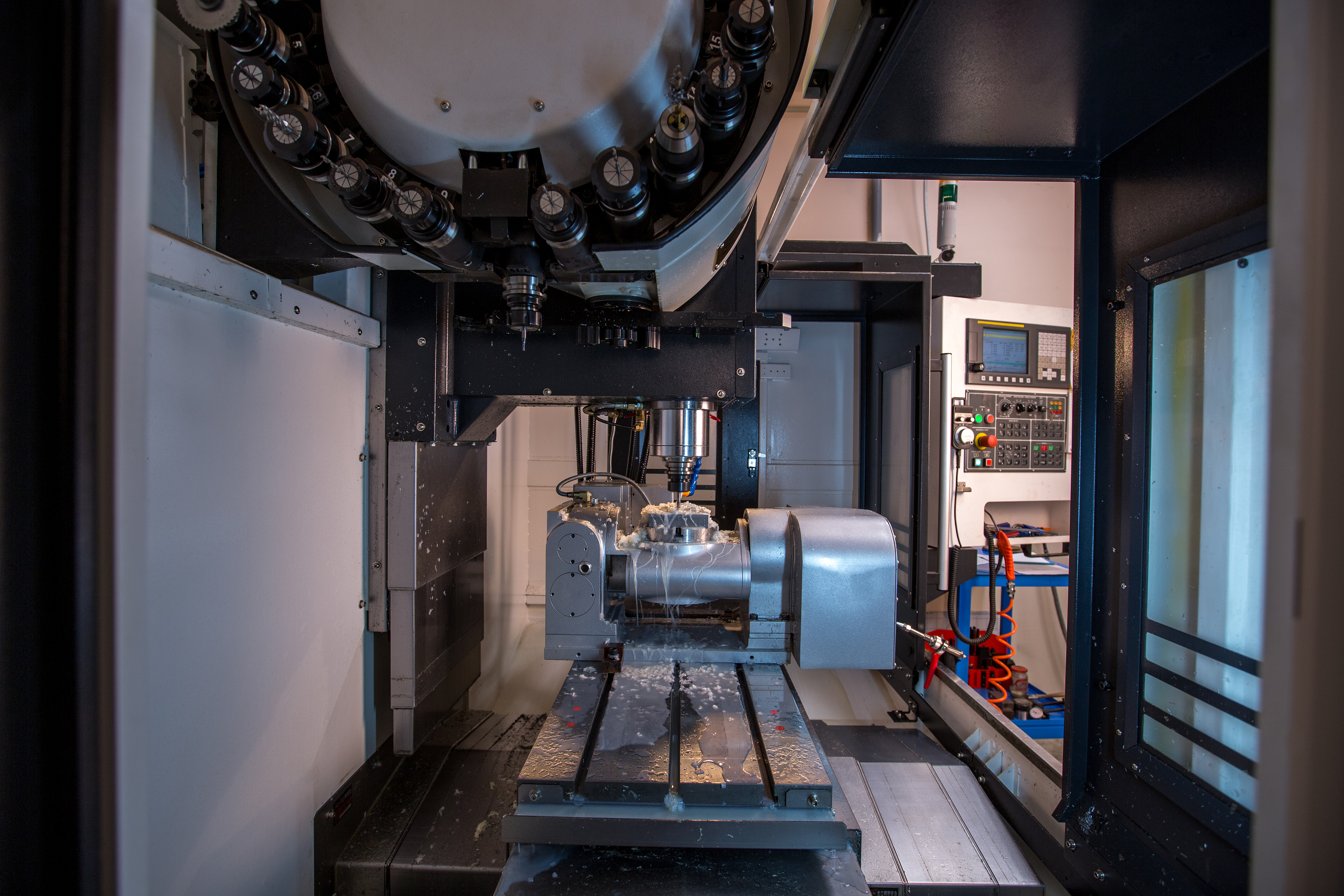
In conclusion, the development history of CNC lathes is a history of continuous innovation and progress. From the early hardwired numerical control systems to today's intelligent numerical control systems, the performance and functions of CNC lathes are constantly improving, providing strong support for the development of the manufacturing industry. It is believed that in the future, CNC lathes will continue to play an important role and promote the manufacturing industry to a higher level.