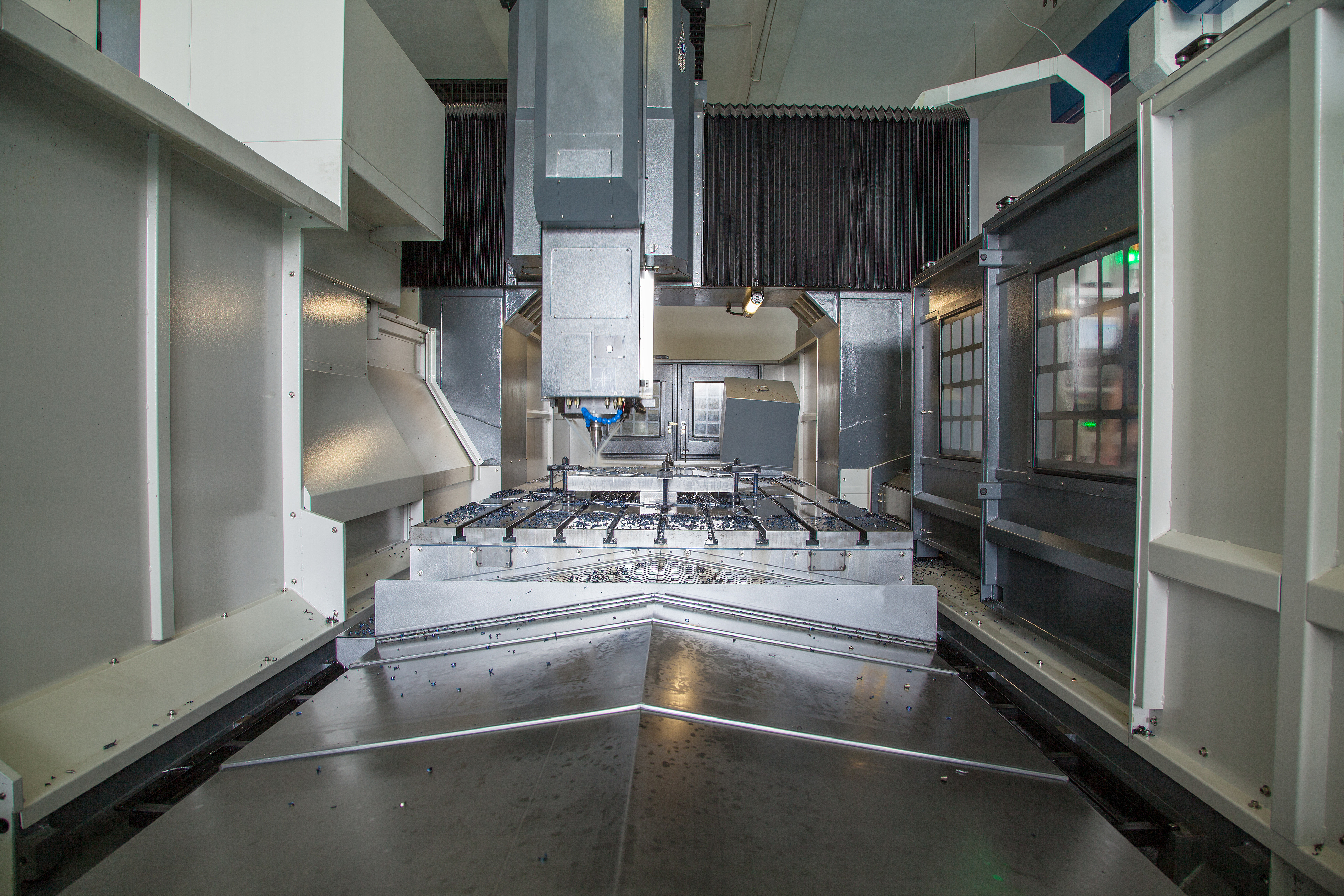
As the "teeth" of machine tool processing, cutting tools directly affect machining accuracy, efficiency, and manufacturing costs. With the requirement for part precision in aerospace, medical devices, and other fields rising to the micrometer level, cutting tool technology is breaking through from traditional high-speed steel and cemented carbide to superhard materials, coating technologies, and intelligent directions. Based on public industry data and technical literature, the following analyzes the innovation path and application practice of cutting tool technology.
Cubic Boron Nitride (CBN): With a hardness of 3000-4000HV, second only to diamond, it is suitable for processing hardened steel (HRC50 and above). Sandvik Coromant's CBN tools can reach a cutting speed of 800m/min in automotive gear processing, which is 5 times that of traditional cemented carbide tools (Source: Tool Engineering, Issue 3, 2024).
Polycrystalline Diamond (PCD): Its thermal conductivity is 10-20 times that of cemented carbide, making it suitable for high-speed cutting of non-ferrous metals such as aluminum alloys and copper. Kennametal's PCD tools have a service life of 50-100 times that of cemented carbide in aerospace aluminum alloy processing (Refer to the industry report of Diamond & Abrasives Engineering).
Coating Type | Technical Characteristics | Typical Application Scenarios | Public Data Support |
---|
TiAlN Coating | Resistant to high temperatures up to 800°C, strong oxidation resistance | High-speed steel tools, milling cutters | Walter's TiAlN-coated end mills have a 2-3 times longer service life (Enterprise technical manual) |
AlCrN Coating | Hardness up to 3500HV, excellent wear resistance | Cemented carbide drills, reamers | Iscar's AlCrN-coated drills improve cast iron processing efficiency by 40% (Industry test report) |
Diamond Coating | Coefficient of friction 0.1-0.2, smooth surface | PCD tools, carbon fiber composite processing | Element Six's diamond-coated tools achieve burr-free processing of carbon fiber composites (Product white paper) |
Cutting Speed: According to Metal Cutting Principles (Harbin Institute of Technology Press), the recommended high-speed cutting speed for aluminum alloys is 1000-5000m/min. When using PCD tools with oil mist lubrication, a surface roughness of Ra≤0.8μm can be achieved.
Feed Rate Control: In titanium alloy processing, Sandvik recommends a feed rate of 0.1-0.2mm/r, combined with an internal cooling system with a cooling pressure of 70-100bar, which can reduce tool crater wear.
Bosch Group adopted an oil-gas two-phase MQL system in engine block processing, where the cutting fluid consumption is only 1/100 of that in traditional wet processing, while the tool life is increased by 20% (Data from Bosch's 2023 Manufacturing Technology Annual Report).
Pratt & Whitney used Seco Tools' CBN inserts in the processing of GTF engine turbine disks, combined with a rigid tool holder system, to achieve high-speed interrupted cutting of Inconel 718 alloy. The processing efficiency was increased by 60% compared with traditional processes (Reported in Aerospace America, April 2024).
Zeiss Medical used Ceratizit's ultra-fine grain cemented carbide tools in the processing of artificial joints (titanium alloy TC4). By optimizing the cutting path, the surface roughness was controlled within Ra0.05μm, meeting the biocompatibility requirements of implants (Enterprise technical case).
Taking aerospace engine blade processing as an example: Although CBN tools (with a unit price of about $500) are 10 times more expensive than cemented carbide tools (with a unit price of about $50), their service life is increased by 20 times, and the unit processing cost is reduced by 30% (Boeing's internal cost analysis report).
Yamazaki Mazak's "Smart Tool" has a built-in RFID chip, which can automatically identify tool parameters and upload them to the machine tool control system, reducing the tool change time to 2 seconds (Data released at the 2024 EMO Exhibition).
Schleifring Group's "CUT DATA CENTER" simulates the cutting process through digital twins, which can optimize the tool path. Actual measurements show that it can reduce trial cutting time by 70% (Industry journal Grinding & Machining, June 2024).
Currently, cutting tool technology has shifted from "passively adapting to processing needs" to "actively defining process standards". When selecting tools, enterprises need to comprehensively evaluate based on material properties (such as hardness and thermal conductivity), processing methods (milling/turning/grinding), and precision requirements. For access to the Tool Selection and Process Matching Manual (compiled based on the ISO 3685 standard), please contact our technical team to obtain the public version of the materials.