On the stage of modern manufacturing, CNC machine tools, with their advantages of high precision, high efficiency, and high degree of automation, have become indispensable key equipment. To fully unleash the potential of CNC machine tools, advanced programming technology and efficient machining strategies are crucial.
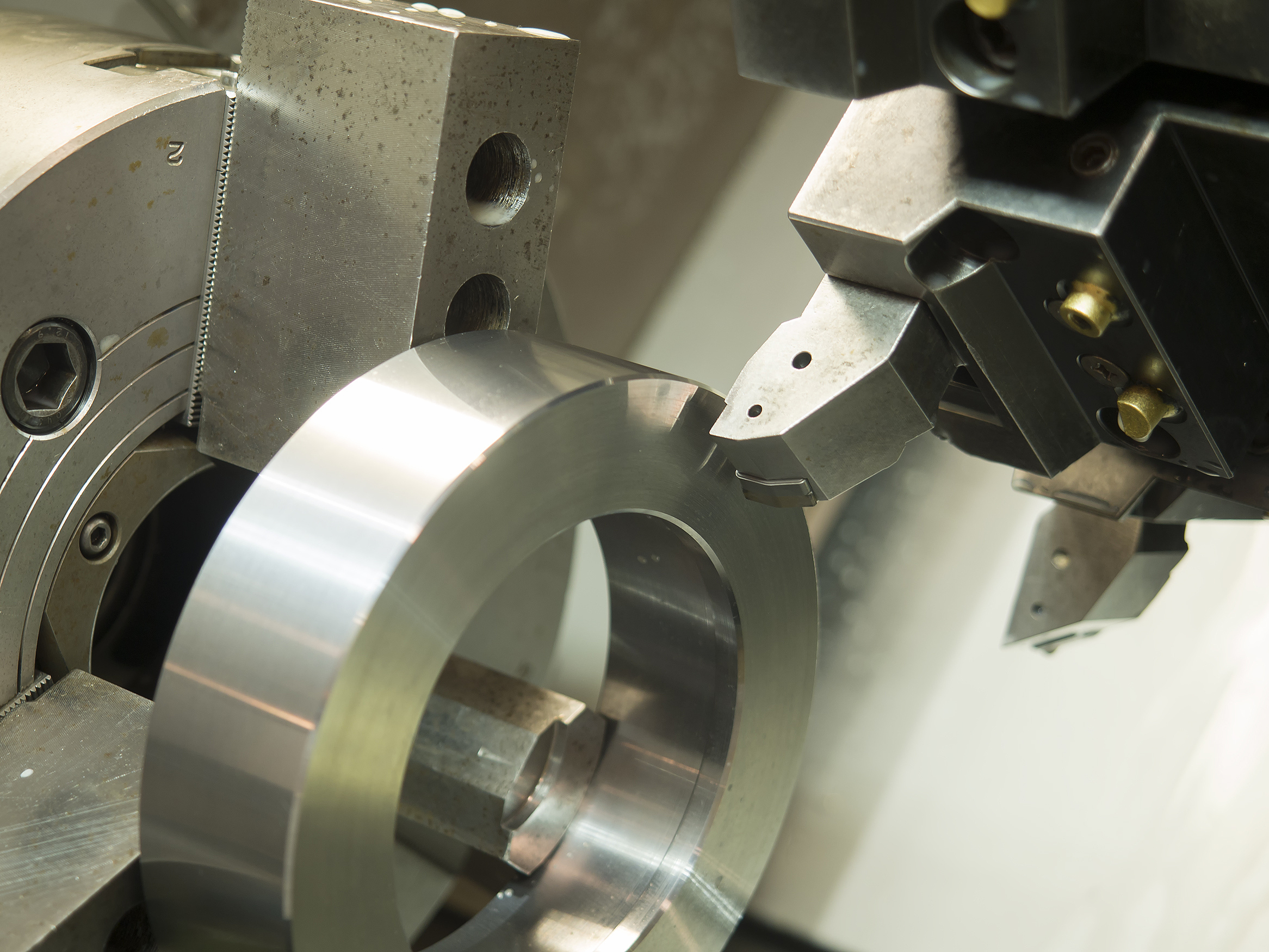
Advanced programming technology is the foundation for CNC machine tools to achieve complex machining tasks. It can precisely control the movement trajectory, cutting parameters, and machining sequence of the machine tool, thereby ensuring the machining of high-quality parts.
Through precise programming, the tool path and cutting depth can be controlled to reduce machining errors. For example, using macro programming can achieve high-precision machining of complex curved surfaces. Macro programs can automatically adjust the tool path according to the geometric shape of the part to ensure that each cut is just right, thereby improving machining precision.
Intelligent programming systems can automatically generate machining programs, greatly shortening programming time. At the same time, advanced programming technology can optimize tool paths, reduce idle travel and repeated cutting, and improve machining efficiency. For example, using high-speed cutting programming technology can significantly increase cutting speed and feed rate while ensuring machining quality, thereby shortening machining time.
For parts with complex shapes and structures, advanced programming technology can achieve multi-axis linkage machining. Multi-axis linkage programming can make multiple coordinate axes of the machine tool move simultaneously, thereby machining various complex curved surfaces and shapes. For example, in the aerospace field, parts with complex curved surfaces, such as aircraft engine blades, often need to be machined. Multi-axis linkage programming technology plays an important role.
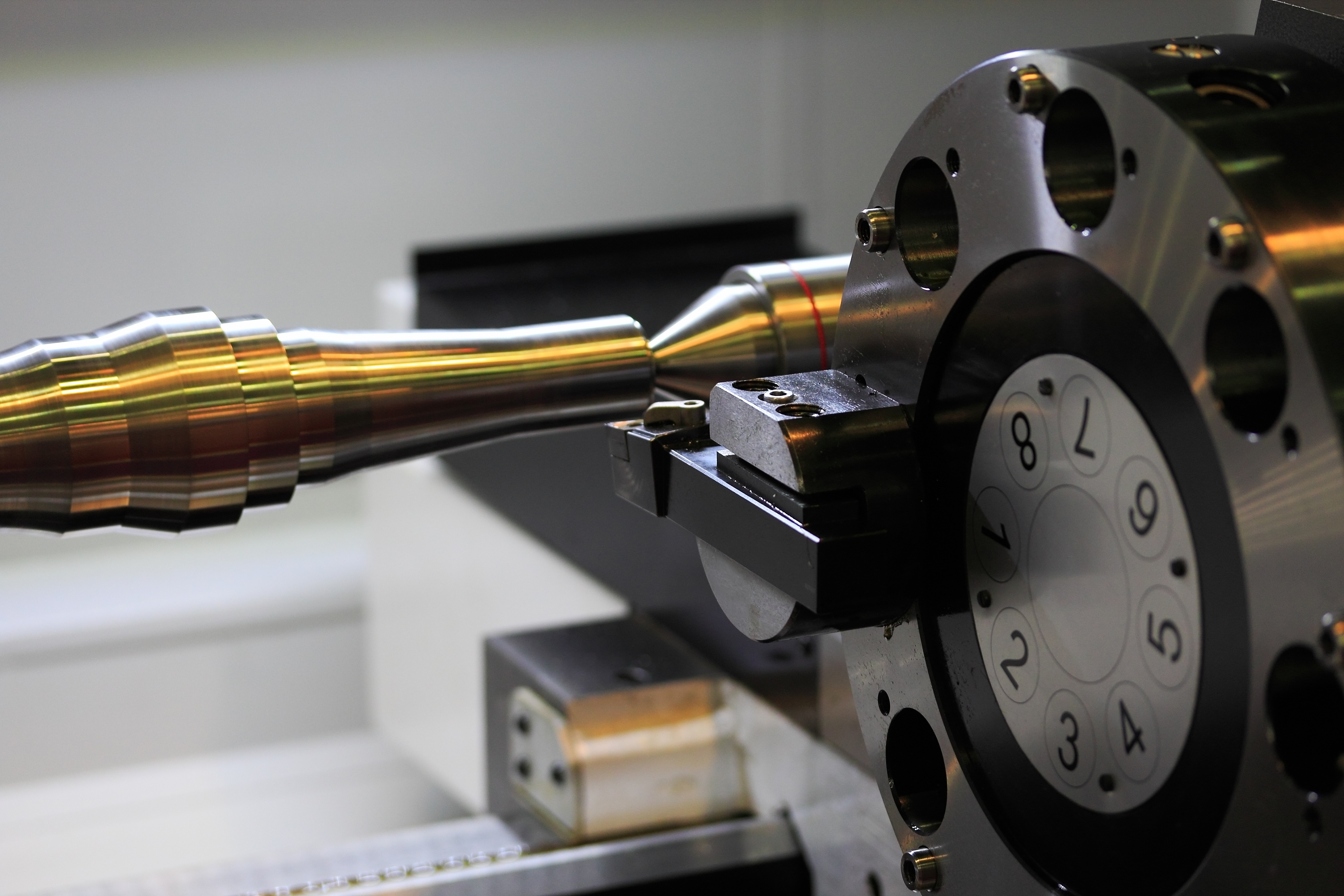
In addition to advanced programming technology, efficient machining strategies are also the key to improving the machining efficiency and quality of CNC machine tools.
The selection of tools directly affects machining efficiency and quality. Appropriate tools should be selected according to the machining material, part shape, and machining requirements. For example, for materials with high hardness, carbide tools should be selected; for parts with high machining precision requirements, high-precision tools should be selected. At the same time, reasonably selecting the geometric parameters of tools, such as tool radius and cutting edge angle, can also improve machining efficiency and quality.
The optimization of cutting parameters is an important means to improve machining efficiency. According to the machining material, tool, and machine tool performance, reasonable cutting speed, feed rate, and cutting depth should be selected. For example, in high-speed cutting, appropriately increasing the cutting speed and feed rate can improve machining efficiency, but at the same time, attention should be paid to controlling the cutting temperature to avoid excessive tool wear.
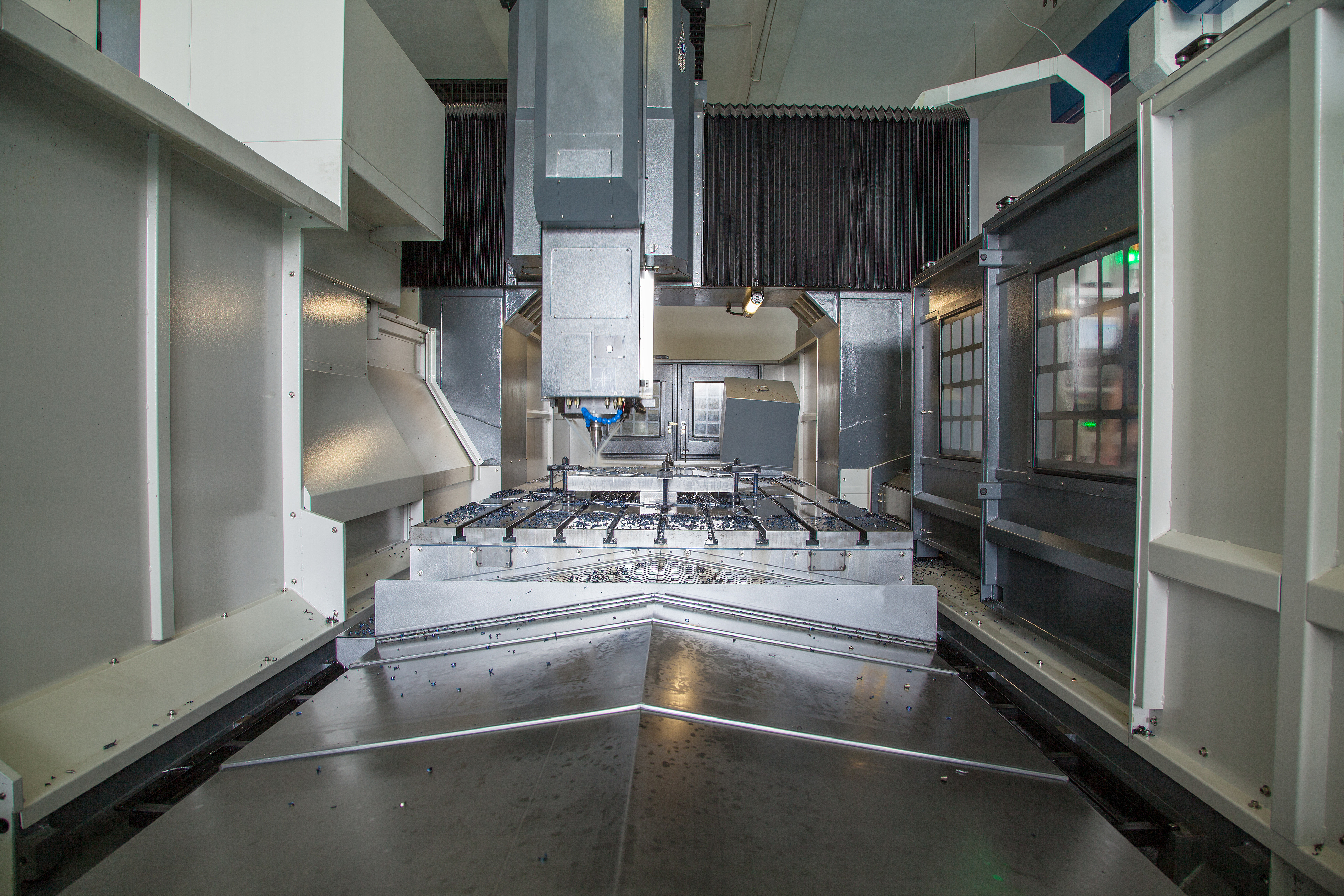
Advanced machining processes can improve machining efficiency and quality. For example, adopting advanced machining processes such as high-speed cutting, dry cutting, and minimum quantity lubrication cutting can reduce cutting force, lower cutting temperature, and improve machining surface quality. At the same time, adopting composite machining technologies such as turning-milling compound and milling-boring compound can complete multiple machining tasks on one machine tool, reduce the number of clamping times, and improve machining efficiency.
The advanced programming technology and efficient machining strategies of CNC machine tools are important supports for the development of modern manufacturing. By continuously exploring and innovating programming technology and optimizing machining strategies, the advantages of CNC machine tools can be fully utilized, machining efficiency and quality can be improved, production costs can be reduced, and greater contributions can be made to the development of manufacturing. In the future development, with the continuous progress of science and technology, the programming technology and machining strategies of CNC machine tools will also be continuously innovated and improved, bringing more opportunities and challenges to manufacturing.