In modern manufacturing, machine tools, as the core production equipment, are crucial in procurement decisions. Whether it is a small - scale processing workshop or a large - scale industrial enterprise, choosing the appropriate machine tool directly affects production efficiency, product quality and the competitiveness of the enterprise.
I. Defining Requirements Clearly
Before starting a machine tool procurement project, the enterprise must have a clear and precise definition of its own production requirements. This includes the types of workpieces to be processed, the size range, material characteristics and the required processing accuracy, etc. For example, if an enterprise mainly produces aerospace components, extremely high processing accuracy is required, and a machine tool with a high - precision control system and advanced tool compensation function may be needed. For an enterprise producing building hardware, while meeting the basic accuracy requirements, more attention is paid to the production efficiency and durability of the machine tool.
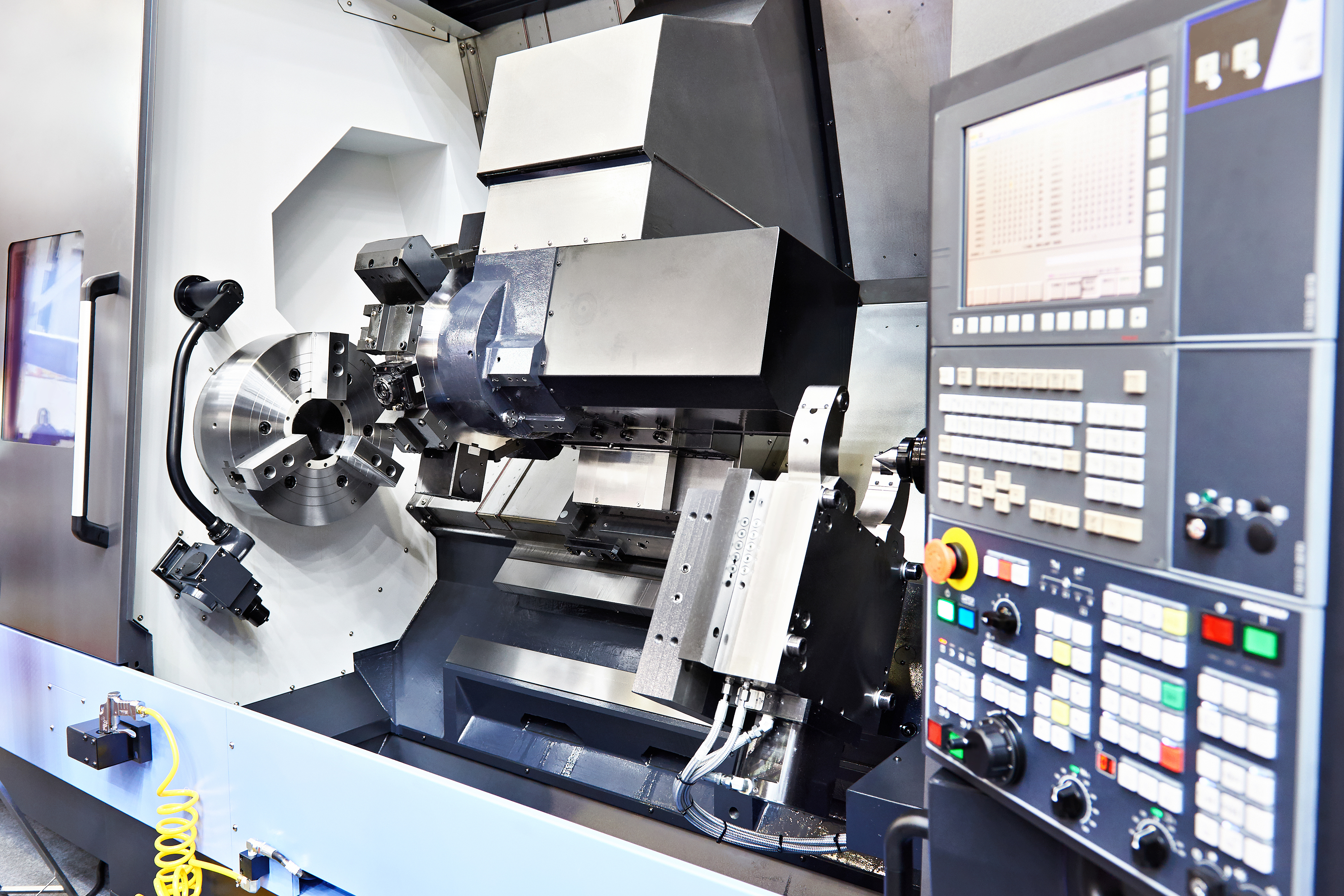
In addition, the size of the production batch also needs to be considered. For large - scale production, machine tools with a high degree of automation and stable production cycles, such as automatic lathes or machining center production lines, are the first choice. For small - batch and multi - variety production, general - purpose machine tools with high flexibility and convenient change - over and adjustment may be more suitable.
II. Selection of Machine Tool Types
Lathes
Ordinary lathes are suitable for processing simple rotary parts, such as shaft - like and disc - like parts. The operation is relatively simple and the cost is low, which is suitable for small enterprises or processing tasks with not particularly high accuracy requirements.
CNC lathes have higher accuracy and a higher degree of automation. They can be processed according to pre - written programs. For complex rotary parts, such as parts with threads, tapered surfaces and eccentric structures, the processing effect is very good. When choosing a CNC lathe, attention should be paid to the functions of its control system, the tool capacity of the tool post and the spindle speed range and other parameters.
Milling Machines
Traditional milling machines rely on manual operation and are suitable for processing planes, grooves and other shapes. CNC milling machines have unique advantages in the processing of three - dimensional complex curved surfaces. For example, in the mold - making industry, CNC milling machines can accurately process complex cavities and cores. When purchasing a CNC milling machine, factors such as the stroke of the coordinate axes, the feed speed and the cutting force should be considered.
Machining Centers
Machining centers are highly integrated machine tools that integrate multiple processing functions such as milling, drilling and boring. For the processing of complex parts, machining centers can reduce the number of clamping times and improve processing accuracy and efficiency. When choosing a machining center, in addition to the basic processing capacity parameters, attention also needs to be paid to the speed and reliability of its tool - changing system, because this directly affects the continuity of processing.
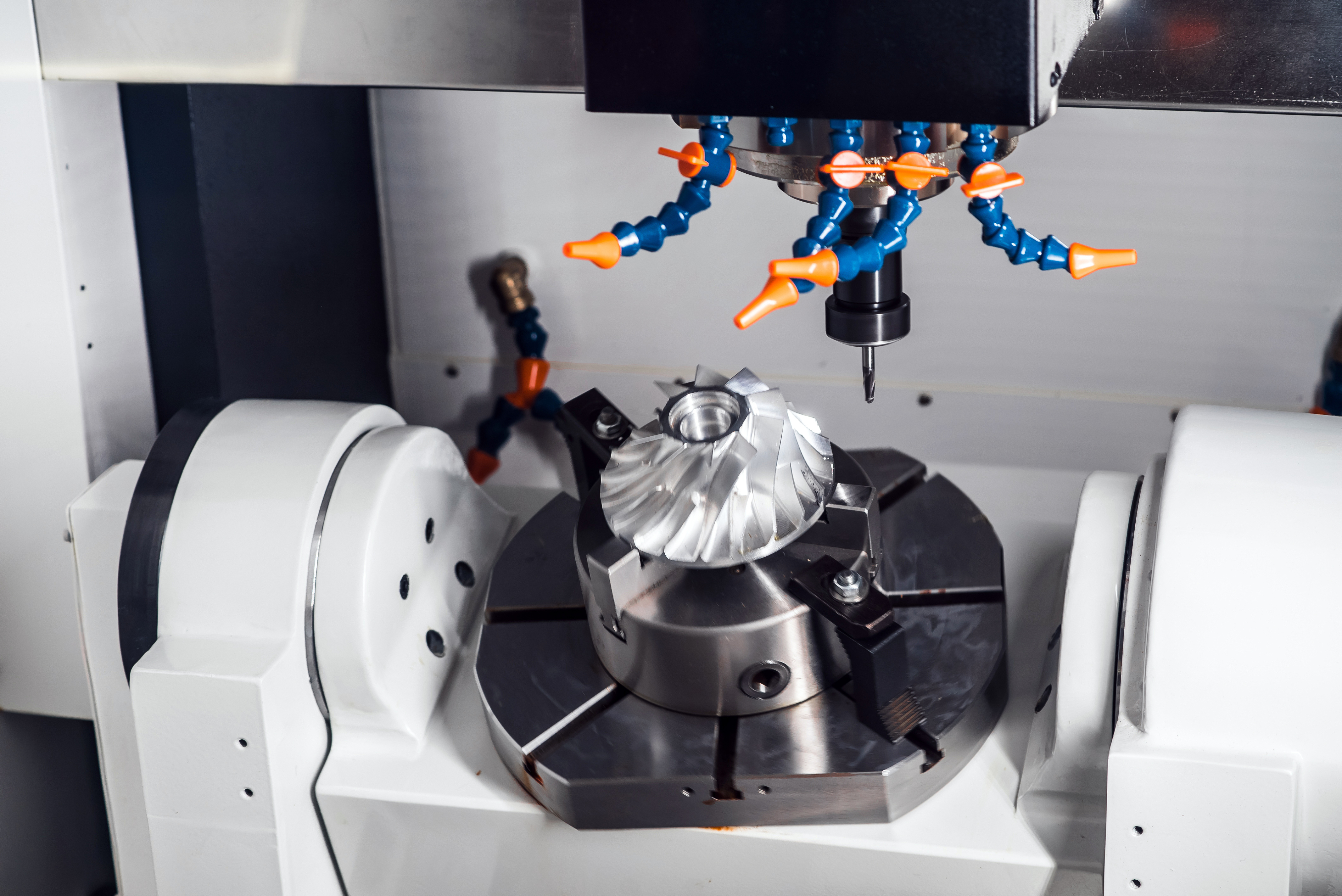
III. Evaluation of Machine Tool Performance
Accuracy
The accuracy of the machine tool is one of the key indicators to measure its quality. It includes positioning accuracy, repeat positioning accuracy and processing accuracy, etc. The enterprise can ask the supplier to provide the accuracy test report of the machine tool, and it is best to be able to inspect the processed samples of the machine tool on - the - spot to intuitively assess whether its accuracy meets the production requirements.
Rigidity
The rigidity of the machine tool affects the stability and cutting ability during the processing. Insufficient rigidity may lead to vibration during heavy - cutting, affecting the processing accuracy and surface quality. The rigidity can be evaluated by looking at the structural design of the machine tool, the material of the bed and the type of guide rail, etc. For example, a machine tool with a cast - iron bed and linear guide rails usually has better rigidity.
Speed and Feed Rate
High spindle speed and large feed rate can improve processing efficiency. However, this also needs to be matched with the power, rigidity of the machine tool and the performance of the tool. When evaluating, according to the actual processing requirements of the enterprise, choose a machine tool with a suitable speed and feed rate range.
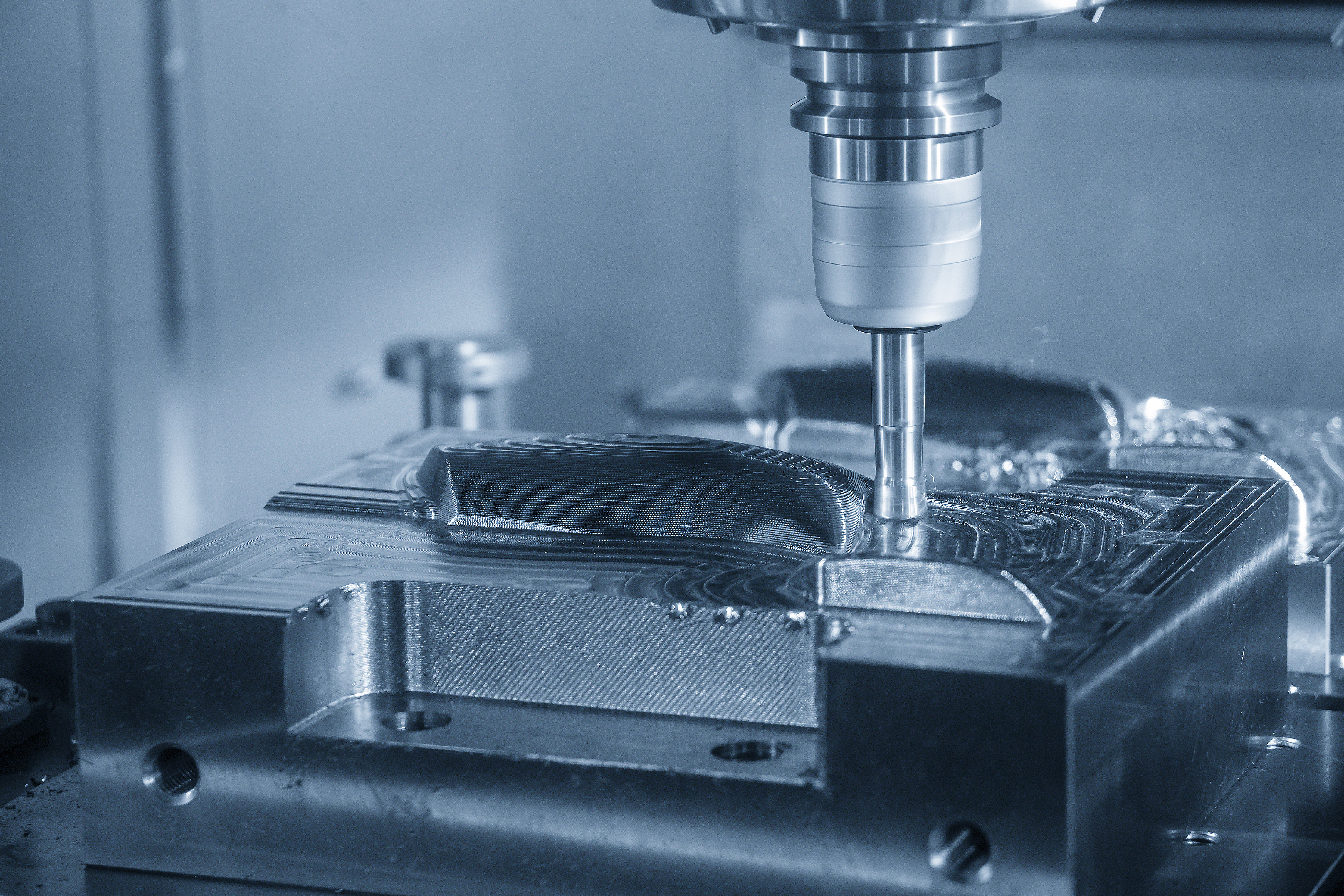
IV. Cost Considerations
Procurement Cost
The procurement cost of the machine tool is the most obvious expense. There are large price differences among different types, brands and specifications of machine tools. When choosing, an enterprise cannot simply pursue low prices, but should comprehensively consider factors such as the performance, quality and after - sales service of the machine tool. For example, although some imported high - end machine tools are expensive, they may have higher accuracy, reliability and a higher degree of automation, and may bring higher production benefits in the long run.
Operation Cost
The operation cost includes energy consumption, tool wear, equipment maintenance, etc. For example, some energy - saving machine tools can save a large amount of electricity cost during long - term operation. And if the tool system of the machine tool has good compatibility and is convenient to replace, it can reduce the procurement cost and replacement time cost of the tool.
Training Cost
If a CNC machine tool is purchased, the training cost of the operator cannot be ignored. The enterprise needs to consider whether the supplier provides comprehensive training services, including operation training, programming training, etc., to ensure that the operator can master the use of the machine tool proficiently and reduce the losses caused by improper operation.
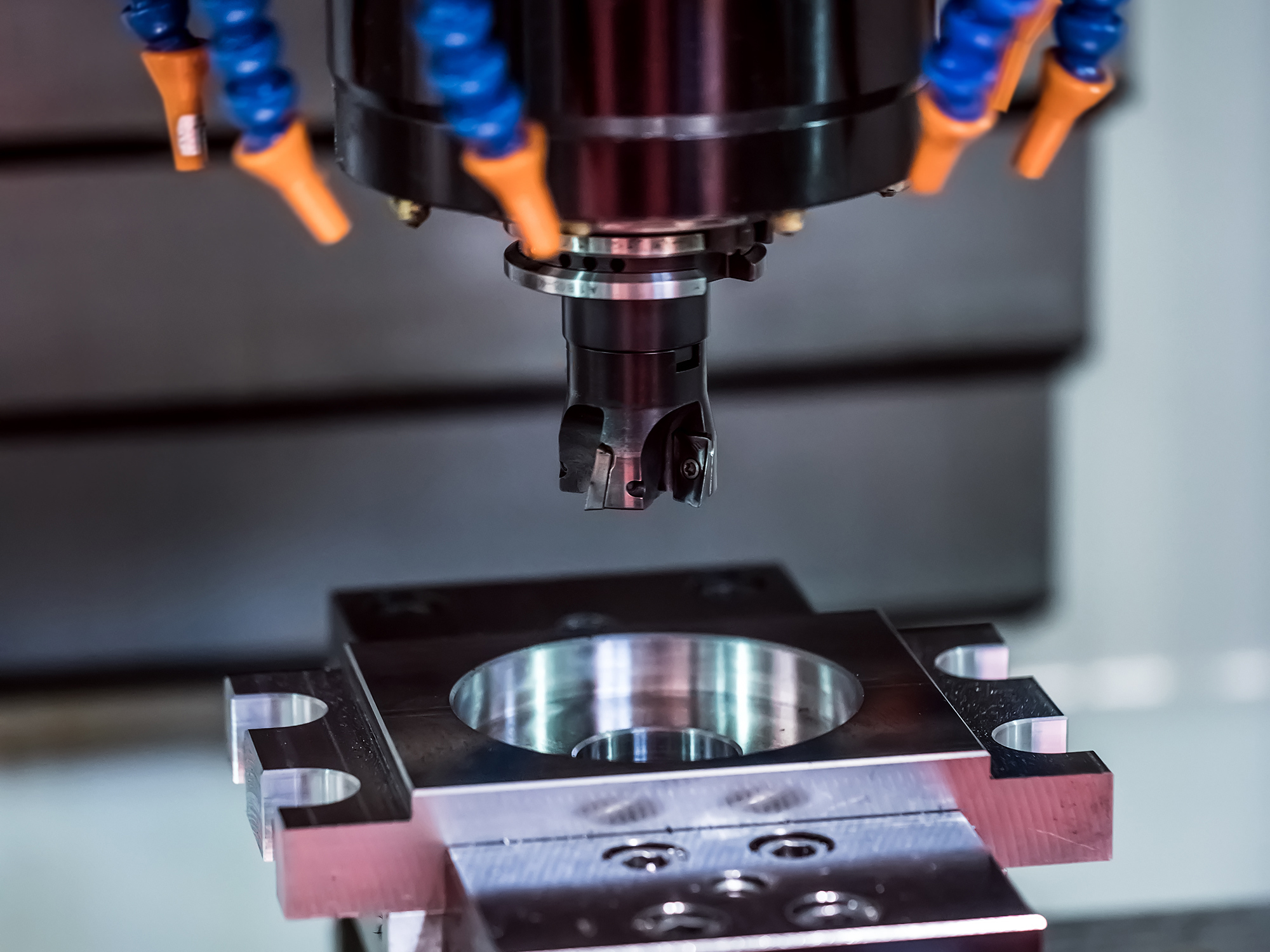
V. Supplier Selection
Reputation and Word - of - Mouth
Choosing a supplier with good reputation and word - of - mouth is extremely important. The reputation of the supplier can be understood by querying industry evaluations, customer feedback, etc. A supplier with a good reputation usually provides high - quality products and reliable after - sales service.
After - Sales Service
Machine tools will inevitably break down during use. Timely and effective after - sales service can reduce downtime and the losses of the enterprise. The supplier should be able to provide rapid - response repair services, sufficient spare - part supplies and regular equipment maintenance plans, etc.
Technical Support
The technical support ability of the supplier is also crucial. In terms of machine tool installation and commissioning, programming optimization, process improvement, etc., the supplier should be able to provide professional technical guidance to help the enterprise give full play to the performance of the machine tool.
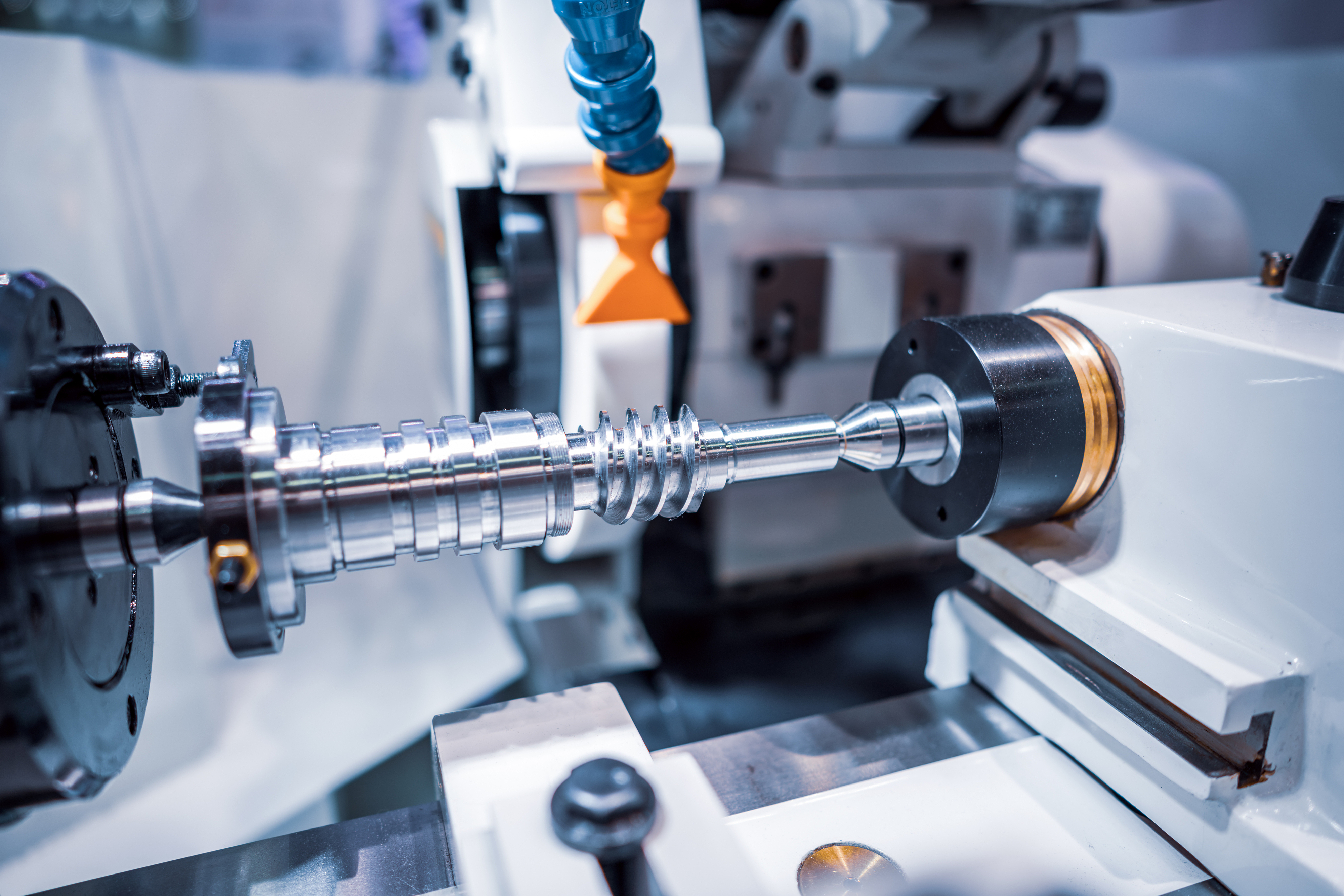
Machine tool procurement is a complex and systematic project. The enterprise needs to make comprehensive trade - offs from demand analysis, machine tool type selection, performance evaluation, cost consideration to supplier selection, etc., so as to purchase a machine tool suitable for its own production requirements and lay a solid equipment foundation for the enterprise's production and operation.